Sustainable Production
When companies better manage their resources and reduce the amount of waste generated from conducting their business, both the environment and their bottom line stand to benefit.
How can they produce sustainably? Some ways include sustainable design, improving resource efficiency, and adopting industrial symbiosis where companies use the waste of others as raw materials for its own operations.
SUSTAINABLE DESIGN
Designing products to be more durable and repairable lengthens their lifespan, delaying their entry into the waste stream. Creating them with materials and components that could be taken apart easily also makes them easier to recycle.
The National Environment Agency (NEA) has been encouraging companies to reduce their packaging waste through the Singapore Packaging Agreement, a voluntary agreement formed in 2007 among the Government, companies, industry associations and nongovernmental organisations.
Now we are stepping up this effort. The NEA will introduce mandatory packaging reporting in 2020 for producers of packaged products and supermarkets and target to implement an Extended Producer Responsibility (EPR) framework for managing packaging waste including plastics no later than 2025.
Companies are also coming together to take action through better product design and processes. For example, as of June 2019, 15 food and beverage (F&B), retail and hospitality companies, including Hilton Singapore, Kraftwich and SaladStop!, have committed to reducing their plastics production and usage by 2030 through the World Wide Fund for Nature’s (WWF) voluntary agreement – Plastic Action (PACT). As part of PACT, over 270 F&B outlets in Singapore have also phased out plastic straws (as of 1 July 2019).
PROMOTING RESOURCE EFFICIENCY
As the world population grows, competition for resources will increase. According to a 2017 report by the International Resource Panel, global material resource use is expected to double between 2015 and 2050 based on current trends.
The report highlighted the need to adopt resource efficiency policies and initiatives, which could save $2.9 to $3.7 trillion a year by 2030. This will also cut resource use by 26% and reduce greenhouse gas emissions by around 20% by 2050.
This global shift towards greater resource efficiency presents opportunities for Singapore companies and industries to be leaders in this area and reap economic benefits.
We are already making headway in improving energy efficiency. For instance, the Energy Conservation Act (ECA) requires large energy users to adopt good energy management practices. This includes conducting regular energy audits, setting up an energy management system, and submitting energy efficiency improvement plans.
Companies also track their materials efficiency through sustainability reports such as those required by the Singapore Exchange of Singapore-listed companies. The reports cover five primary components: (a) material Environmental Social Governance (ESG) factors, (b) policy, practices and performance, (c) targets, (d) sustainability reporting framework and (e) Board statement.
However, the commercial and industrial sector still contributes around half of total waste disposed of. Material and waste audits can thus allow companies to identify opportunities for reduction through a systematic evaluation of material flows and costs, and develop concrete plans to improve material efficiency. We will be exploring means to support more companies to do this.
At the same time, the Sustainable Manufacturing Centre (SMC) of the Agency for Science, Technology and Research (A-STAR) aims to promote sustainability in the manufacturing industry by bringing industry associations and the research community together to work with Government agencies to develop and implement sustainable manufacturing technologies.
TWEAKS IN PACKAGING SAVES COMPANY MATERIALS AND MONEY
By making a crucial material swap, a packaging company helped its client save money.
Instead of packing its client’s product – a Field Replacement Unit (FRU) – in a polypropylene moulded case, Greenpac (S) Pte Ltd designed a paper carton box with polyethylene foam which did the job just as well.
This reduced the overall weight of packaging from 5 kg to 1.5 kg, saving 53,000 kg of packaging material and $6,000 in material costs per year.
This, and several other initiatives, won Greenpac an Excellence Award (SMEs) at the Singapore Packaging Agreement Awards in 2017.
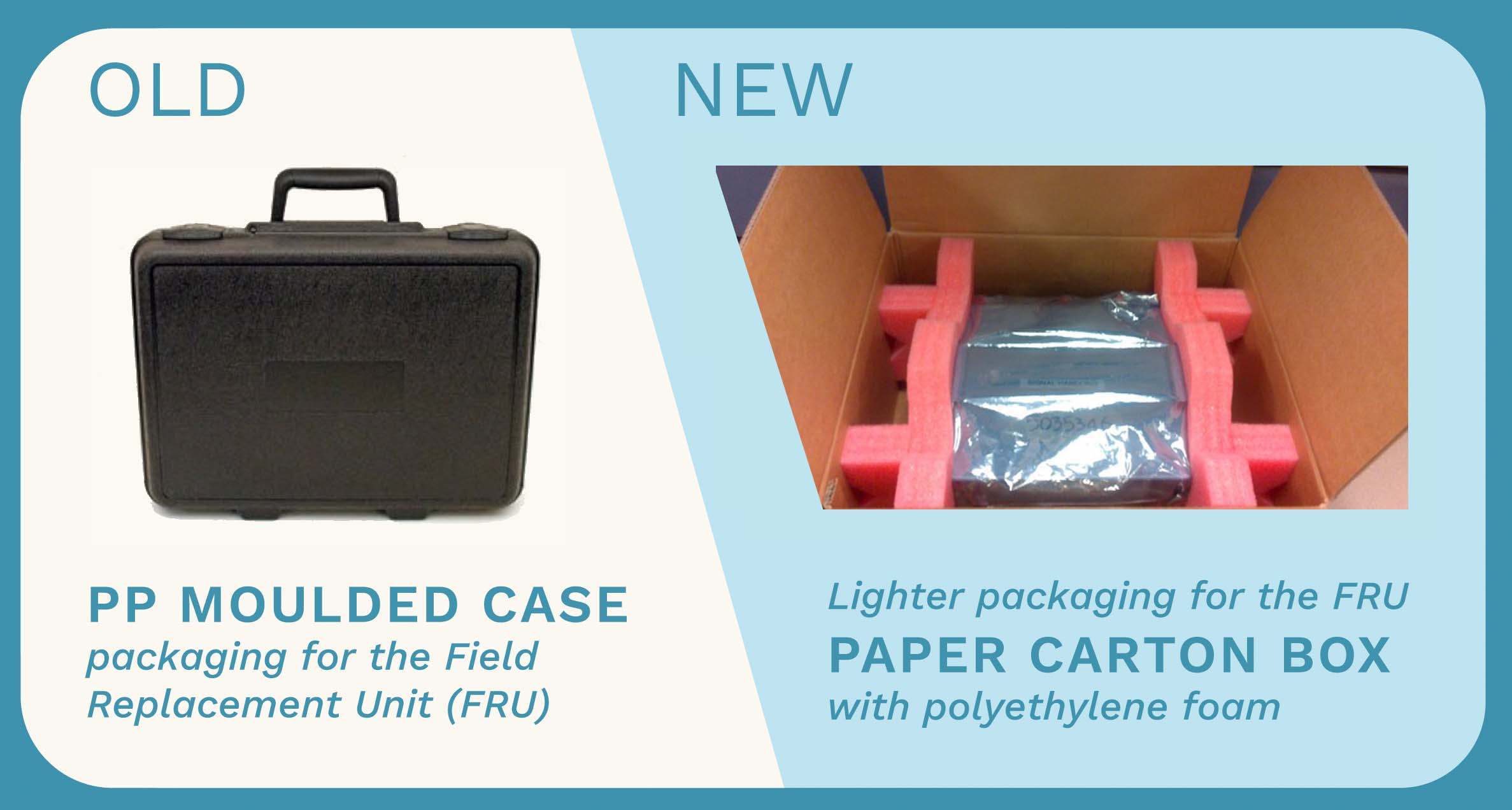
BRINGING TRANSFORMATIVE TECHNOLOGIES TO THE INDUSTRY
The Model Factory @ Advanced Remanufacturing and Technology Centre of A-STAR offers capabilities and expertise in three areas underpinning smart manufacturing. It provides companies with a platform to learn how technologies are implemented in manufacturing use-cases or test process improvements without disrupting their own operations.
Secure connectivity and intelligent system
Real-time analytics allows for decentralised decision making, while condition monitoring provides data for predictive model and optimisation. Together, they make factories more intelligent, and in turn more agile and efficient.
Virtual manufacturing
With a full digital footprint of a factory, every machine and process will generate real-time information that will provide the data required for optimisation, decision-making, planning and learning. Meanwhile, virtual design will shorten the product design life cycle and the need for physical prototypes. The use of augmented reality will help in training operators and machine maintenance.
End-to-end solutions
The end-to-end digital thread, from customer-specific orders, product design and manufacturing to aftersales service, provides seamless data exchange and new business opportunities. These digital threads also enable better supply chain management and management of distributed manufacturing assets globally.
PROMOTING INDUSTRIAL SYMBIOSIS
Industrial symbiosis refers to mutually beneficial collaborations, where what is deemed as waste by one company could be raw material for the operations of another. This leads to more sustainable industrial processes and cost savings.
To optimise such alliances, both entities are typically sited within close proximity to reduce transportation costs, and their infrastructures are carefully designed.
Industrial symbiosis can also be applied to brownfield sites, where waste-resource flows are matched by an independent organisation. The Finland Industrial Symbiosis System (FISS) is one example. To date, there are around 600 companies and 4,700 resources involved in the FISS.
In Singapore, industrial symbiosis is illustrated through the design of the Tuas Nexus, where the NEA’s Integrated Waste Management Facility will be integrated with PUB’s Tuas Water Reclamation Plant. Output from one facility will be used as feedstock to another, while keeping the land use footprint and environmental impact to a minimum. (See Chapter 4 for more details on Tuas Nexus.)
Similarly, at upcoming districts such as Jurong Lake District and Punggol Digital District, Government agencies across various domains are working together to optimise resource flows and minimise transport within the district. For example, we are exploring closing waste loops at the district level, such as by converting food waste into useful products like compost, which can be used for landscaping.
STUDYING THE CIRCULAR ECONOMY ON JURONG ISLAND
Singapore is home to Jurong Island – one of the top 10 chemical parks in the world and a key anchor for Singapore’s energy and chemicals industry. It is an example of industrial symbiosis, facilitated by shared infrastructure and an inter-connected industrial cluster. To remain competitive, Jurong Island companies have been seeking to optimise resources, such as water and energy, and also to minimise waste in their own plants.
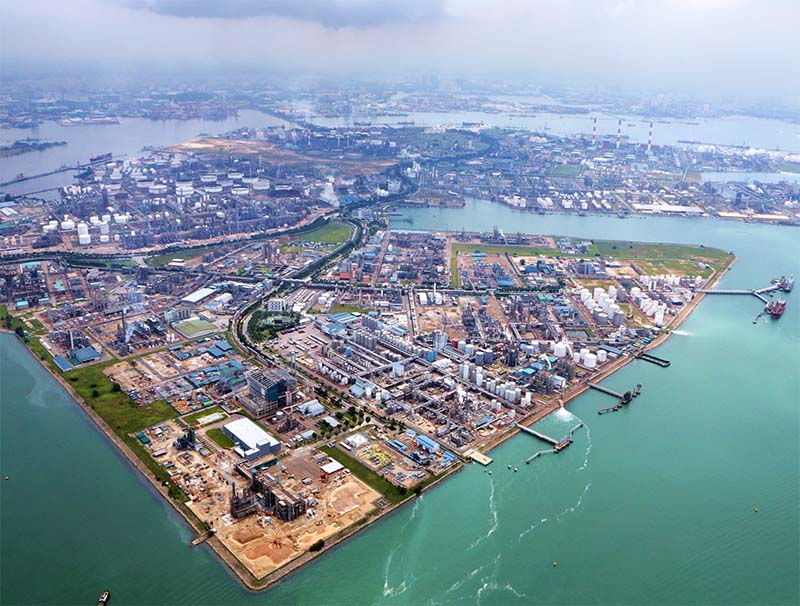
The close proximity of related industries on Jurong Island provides an ecosystem where one company’s product can become the feedstock of another. For example, waste from some companies is burnt to generate steam for industrial use. Similarly, wastewater is recovered and recycled for industrial use.
However, there are limitations to the efforts by individual companies. Increasingly, companies are recognising the importance of collaboration so as to jointly discover opportunities for further resource optimisation at the systems level.
To deepen this industrial symbiosis, companies on Jurong Island have come together to support a study commissioned by JTC Corporation (JTC) – the Jurong Island Circular Economy Study. The study seeks to bring about environmental and economic gains for companies by mapping out the current water, energy, and waste flows on Jurong Island, and to identify further synergies and reduce resource use at the systems level.
It is the next step towards positioning Jurong Island as an economically and environmentally sustainable chemicals park. The study is ongoing, with recommendations targeted to be ready in 2020.